Design and analysis of roller bearing cages
IN COLLABORATION WITH JTEKT KOYO, Clemson researchers advanced the fundamental understanding of material and process dynamics for optimal design of a bearing’s polymeric cage.
PROCESS DYNAMICS
JTEKT North America is a leader in automotive bearings. It has been a part of the Clemson University International Center for Automotive Research since 2006.
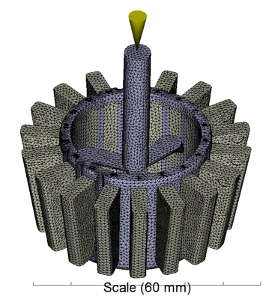
OBJECTIVES AND PARTNERSHIPS
MAIN TASKS
- MATERIAL SELECTION and process physics optimization
- Design of the cage geometry
- Material selection
- Design of the mold
- Fabrication of the mold
- Injection molding of cage
- Injection molding of tensile specimens
- Characterization and testing
- EFFECT OF FLUID such as moisture and oil on the properties and geometrical dimensions of polymeric cages
- FORCE COMPUTATION for assembly/disassembly of rollers in cage by modeling the geometry of the cage and the deformation mechanism. The required force to push out the roller from the cage was calculated according to the stiffness of the cage material.
PARTNERS
- Koyo
- JTEKT Corporation
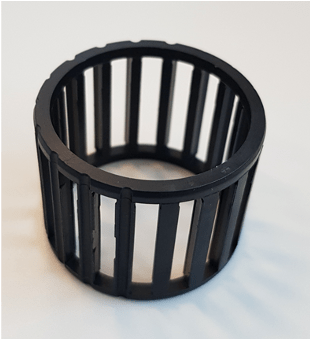
PARTNERS
- Koyo
- JTEKT Corporation