SET IN MOTION
LEADING EDGE
Every project has distinctly unique designs and engineering needs. The Clemson Composites Center (CCC) provides comprehensive services across all levels of advanced materials integrations. From synthesizing custom materials for functional prototypes to developing scalable, integrated manufacturing plans, the Center can offload, supplement, and drive results for businesses seeking to grow with portfolios in composite structures.
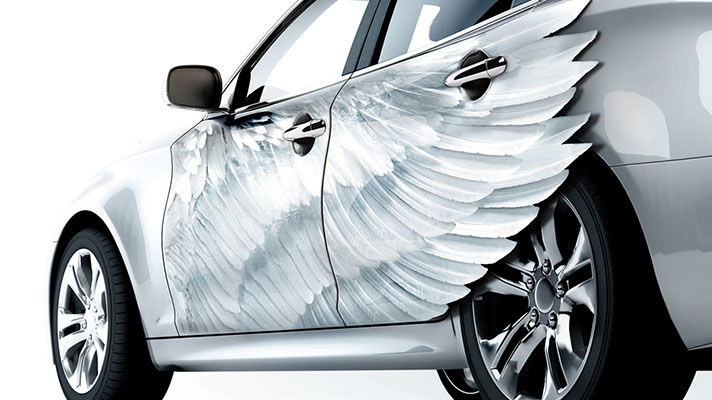
When it comes to automobiles, the future is dancing ever closer to the present.
– Yunyi Jia, McQueen Quattlebaum Assistant Professor
Clemson strives to be a productive turnkey solution to your organization’s challenges, demanding little supervision while achieving quality results. In addition to foundational research and basic science, CCC offers rapid prototyping for form and fit, complete with design and manufacturing pathways for maximum impact.
The Center, an ITAR-compliant design and engineering facility, has the capability and experience to manufacture using most composite processes and a variety of composite materials within its state-of-the-art $6M lab space. Experts can develop the right manufacturing strategy as well as perform comparative processing studies to find the best solution for your product. These services are complemented with an onsite, fully equipped test and inspection laboratory and certified personnel.
01
SERVICES
DESIGN & ENGINEERING
Public, private and academic partners turn to CCC to transform their ideas into working products that efficiently mesh with existing manufacturing systems, engineering processes and compliance regulations.
30+ YEARS EXPERIENCE
With 30+ years of combined design and functional prototyping experience, advance your project from TRL 1 to 7 and beyond.
CCC’s team includes world-class experts with deep expertise in product development, advanced CAE simulation, composites processing, tool design, systems integration, virtual manufacturing planning, and crash testing. With 30+ years of combined design and functional prototyping experience, advance your project from TRL 1 to 7 and beyond.
The CCC team spearheads the product development process with a systems approach and in close collaboration industry.
Experienced engineers and designers specialize in digital life cycle management, ensuring your product has the best chance of succeeding. Our team is an agile, productive partner in your development strategy, demanding little supervisory time but delivering high-quality results that advance your business needs and meet your deadlines.
- Lightweighting strategy analyses at the vehicle level.
- Benchmarking.
- Plant layout design.
- Tooling design.
- Quality debugging.
- Life cycle assessment.
- Component redesign and lightweighting.
- Production runs for functional prototypes.
- Finite element simulation support.
- Virtual manufacturing simulation.
Using industry standard simulation tools and software, the center’s experts offer advanced numerical and analytical modeling for all range of mechanical phenomena from material synthesis and development to manufacturing processes and final product assessment.
Proven with industrial and public projects such as the Center’s $5.8M concept-to-commercialization ultra-lightweight door project, CCC provides a variety of modeling and simulation services for industry.
- ANALYTICAL MODELING: Isolate and understand your project’s every geometry within a simulation with an incredible degree of accuracy.
- NUMERICAL MODELING: Tackle complex geometries and integrated systems problems for advanced industrial simulations.
A product is only as useful as its tooling design, a crucial step done in parallel with the overall product design process.
The Center offers specialized tooling design and fabrication for plastics and composites manufacturing within a wide variety of industries. CCC offers tool design and manufacturing as part of turnkey projects or as a separate service bundled with prototyping, tool testing and modification.
We minimize surprises with highly accurate material characterization for long-term product viability.
CCC offers material card generation and coupon-level testing using industry standard protocols (ASTM/DIN/ISO/EN) needed to characterize material’s performance in tensile, compressive, shear and bending conditions. As our foundational service, our expertise stems from characterizing both static (MAT 8) and nonlinear (MAT 54) material behavior.
02
SERVICES
MATERIAL DEVELOPMENT
Reach a new level of customization with Clemson’s deep expertise in the design and synthesis of new polymers and advanced composites — created specifically for your product.
FULL SUITE ANALYSIS
Clemson Composites Center’s full suite of chemical and mechanical analysis puts newly synthesized materials through their paces, allowing an iterative approach to property enhancement.
The Center enhances the sustainability of traditional polymers with bio-based sources and nontoxic protocols and offers an overall sustainability assessment for new polymer designs as compared to traditional synthetic pathways.
Our facilities include a full-scale chemistry laboratory allowing the lab-scale synthesis of new polymers. With a full-time lab consultant, Clemson uses data to advise on the use of catalysts, feedstocks, and processing conditions to tailor new materials for specific properties.
CCC’s expertise extends to the replacement of traditional feedstocks for polymer synthesis to renewable, bio-based sources. The world-class research team can help incorporate agricultural feedstocks or other agricultural byproducts into new polymer protocols with the corresponding tests to verify satisfactory physical properties.
Traditional melt-processed recycling creates a downgraded material incapable of use after several cycles.
The use of chemical recycling, on the other hand, up-cycles waste material by reverting waste material back to molecular building blocks capable of resynthesis into high-performing materials. The application of chemical recycling envisions a truly circular economy where waste material is used as a feedstock for next-generation material development.
Life Cycle Assessment (LCA) is used to determine the environmental impacts of a material during raw material extraction, manufacturing, use and disposal.
The impacts of using bio-based or less toxic precursors for polymer synthesis can be compared to the traditional synthetic pathway using LCA. Strategies for a material’s end of life can also be evaluated using LCA to determine the environmental gains of different recycling strategies.
The Center offers extensive experience with the thermochemical transformations of bio-based materials that lead to development of highly porous products used in water and air purification applications, energy storage devices, and others. Capabilities include pyrolysis, carbonization, thermoreduction and torrefaction using inert gas or mixed-gas environments.
Foams offer infinite possibilities for novel products in material development.
Clemson designs structural composite foams with customized cell structures and properties using strategic nucleating agents, which provide a heterogeneous interface to reduce the nucleating energy barrier. Our expertise includes carefully engineered nucleating agents to control and regulate foaming behavior for optimal cell morphology and properties.
Polymer blending allows for unique product properties that would be otherwise impossible or less economical than a single polymer. Clemson offers complete polymer blend design in conjunction with manufacturing design to produce advanced plastics for specific customer needs.
Equipped with a knowledgeable team of experts, Clemson offers innovative solutions for the design, synthesis, and processing of various materials based on the costumers’ needs. This includes state-of-the-art approaches to utilize biorenewable resources for the development of nonarchitectural products with required characteristics and performance.
- Filler Sizing
- Fundamental Chemistry Development
- Material Processing
- Material Synthesis
- Mechanical and Thermal Analysis
- Nucleating Agents
- Pilot-Scale Injection Molding
- Polymer Blend
- Twin Screw Extrusion
- Filler Sizing
- Fundamental Chemistry Development
- Material Processing
- Material Synthesis
- Mechanical and Thermal Analysis
- Nucleating Agents
- Pilot-Scale Injection Molding
- Polymer Blend
- Twin Screw Extrusion
03
SERVICES
MANUFACTURING
Clemson Composites Center is committed to streamlined product development and functional prototyping based on holistic, cost-effective manufacturing process plans for instant application.
PROVEN APPLICATIONS
The Center is home to one of the most versatile and complete suites of thermoplastic and thermoset polymer processing options under one roof.
Designed with flexibility and interoperability in mind, state-of-the-art infrastructure supports traditional as well as innovative hybrid procedures that historically were inaccessible. Proven with industrial and public projects such as the Center’s $5.8M concept-to-commercialization ultralightweight door project, CCC offers a broad array of advanced manufacturing and functional processes, including manual and automated injection, compression, forming and continuous processes.
Thermoforming is a manufacturing process in which a plastic sheet is heated to a pliable temperature and placed over a male or female mold. Afterward, a vacuum is applied to draw the plastic sheet and manipulate it into the shape of the mold.
The advantages of thermoforming are the adaptability to a customer’s design needs. A quick way for prototyping, it is a relatively lower cost process, and the final products are aesthetically pleasing and customizable in color. However, they cannot be used for manufacturing shapes that are very complex. Thermoforming has a widespread application from toys to the permanent surfaces of automobiles. One of the most common uses is the packaging of food and consumer goods.
CCC has both the expertise and equipment to help industry from the material development, design, and analysis step to the manufacturing processes optimization and product quality assessment.
High-pressure resin transfer molding (HP-RTM) is a modernization of conventional resin transfer molding (RTM). HP-RTM combines hot compression molding with resin injection. A dry pre-consolidated preform is inserted into the mold mounted in the press. Once the press is closed and at the right temperature, the specifically developed HP-RTM resin is injected, filling the tool and flowing all throughout the preform. HP-RTM processes allow for lower cycle times, excellent structural performance, complex geometries, and highly automated production. Typical applications of HP-RTM are serial manufacture of automotive body structure components such as floor pans, sidewall panels, crush cans, and bulkheads.
CCC houses an automated HP-RTM machine with a 1,000-ton press, as well as an advanced doser unit to support research and development for large-scale industrial production. Designed with industry equivalents in mind, Clemson’s HP-RTM results can be directly applied to manufacturing floors today.
Wet compression molding is a composites molding process where resin is applied to the top of a fabric blank. The wet blank is then transferred to the bottom tool in a set of matched molds and compression-molded in a press, which pushes the resin into the fabric.
The key advantages of wet compression molding include the ability to apply resin outside of the mold; this frees up equipment for reduced cycle time and speeds resin impregnation versus the injection process required for resin transfer molding (RTM). The process typically eliminates the preforming step, proceeding directly from wet fabric to a molded part. However, the process is best suited for flatter parts and fewer complex geometries. Both the blank and tooling must prevent wrinkles or other defects during molding. Wet compression molding represents a more economical alternative to high-pressure RTM (HP-RTM).
- Eliminating resin injection allows application of resin while other parts are curing in the press.
- The resin, usually epoxy, can also be more reactive because no latency is required to postpone cure until the RTM mold is filled.
- Pressing multiple components at once reduces molding cycle time and increases further productivity.
We offer full guidance for industries from the very first steps to the final products. We have the experienced expertise and all the tools required to help you improve your processes and/or product quality.
Injection molding is one of the most cost-effective and versatile ways to manufacture plastic and composite parts for medium-to-high volume production in a variety of materials, colors, and configurations. CCC offers a wide range of injection molding services (up to 1478 cm3 shot volume) based on the injection unit bolted next to the 1,000-ton vertical press. This equipment was integrated with Supercritical Fluid (Sc.F.) assisted technology to perform foam injection molding process. There is a separate set of barrel system available for processing Long Fiber Thermoplastics (LPT) with a variety of reinforcements and matrix systems.
In addition to this equipment, a lab-scale injection molding machine was available for research and producing coupons and plastic parts up to 69 cm3 volume. This machine was also equipped with a Sc.F. assisted molding system enabling more in-depth research on plastic parts with microcellular structure.
The back-injection molding of sheet metals with plastics is our expertise. We use our knowledge in the forming of materials and the system for the application of bonding agents, which we design ourselves.
Extrusion is a continuous process to develop a thermoplastic system by blending the polymers, fillers, and other additives to enhance the properties of the plastics. CCC hosts an extrusion line consisting of a 24 mm Krauss-Maffei twin-screw extruder (L/D ratio= 42:1) with a maximum conveying rate of 305L/h. Our twin-screw equipped with two gravimetric feeders (main and side feeders) and dual-injector ports. The twin extruder is hooked up to a standard pelletizing line. Our extrusion line is host to an array of sensors capable geared toward inline quality control with efforts to establish in introduction line crystallinity monitoring.
The vacuum infusion process uses atmospheric pressure to push the thermoset resin into the mold cavity containing pre-laid fiber mats. The mold cavity can be a one-sided mold with bagging film being utilized for the “B” side, a two-sided mold, or even a soft “envelope” bag.
The process is highly controllable, due to it being governed by the principles of Darcy’s Law. This means that there are only three variables affecting the flow of the resin: (1) permeability of the laminate, (2) viscosity of the resin, and (3) pressure differential in the cavity in relation to atmospheric pressure. If all three variables are unchanged, then the infusion process will consistently flow the same way with every injection for a given part. CCC has used the vacuum infusion process to manufacture low-cost prototypes for several projects like the DOE Door project.
CLEMSON COMPOSITES CENTER INCORPORATES a complete path from concept to product launch that encompasses Research, Innovation, Application Development, and Workforce Education. Proven with industrial and public projects, CCC offers a broad array of advanced manufacturing and functional systems, including manual and automated injection, compression, forming, and continuous processes.
REVOLUTIONARY
A substantial component of the Center is to integrate traditional learning with that of innovation campuses. This integration contributes to cost-effective, efficient, and sustainable technologies within manufacturing.
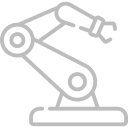

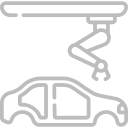
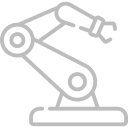

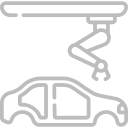
04
SERVICES
CHARACTERIZATION
Backed by a group of global experts, CCC’s characterization team provides detailed analyses of products and components to ensure comprehensive understanding and quality control for advanced materials.
EXPERT-BACKED RESEARCH
Characterization services include thermal and chemical materials, material testing and materials database generation, sub-assembly testing and validation, component testing, and NADCAP-compliant mechanical property testing. The Center caters to the aerospace, automotive, consumer, medical and defense industries with a variety of lay-ups, prepregs, resin systems, adhesives, and reinforcements available.
The polymer and material synthesis capabilities of the CCC are complemented by a comprehensive approach to chemical and molecular structure determination. To explain the chemical structures and environments of novel materials, a comprehensive suite of NMR, FTIR, GPC, and other spectroscopic techniques are used. The CCC collaborates with many other state-of-the-art characterization labs enabling a more thorough analysis when traditional techniques are not sufficient.
CCC is home to a one-of-a-kind Universal Testing Machine designed for advanced composites testing at both the coupon and component level for evaluation at room, elevated and cryogenic temperatures. Mechanical testing systems offer data about tensile, compression, bend, peel, shear, tear, and cyclic tests to validate and ensure the quality of engineering designs.
The Center offers the full spectrum of thermal analyses for a wide range of materials, including differential scanning calorimeters (DSC), rheometry, thermal mechanics and thermogravimetrical analysis. Thermal analyses provide insight into the behavior of polymers under various conditions during processing, supporting the optimal production, end-use performance, and composition of advanced material components.
CCC includes several state-of-art high-resolution transmission electron microscopes (TEM), scanning electron microscopes (SEM), and a combined Focused Ion Beam (FIB)/SEM microscope. We frequently utilize Energy Dispersive X-ray Spectroscopy (EDS), Electron Backscatter Diffraction (EBSD), Wavelength Dispersive Spectroscopy (WDS), sample manipulation and surface modification capabilities installed on these electron microscopes. Experienced researcher engineers oversee each technology to maximize value and insight.
The Center has capabilities for testing composite components and subcomponents in a variety of unique load cases. Our Instron 5980 UTM is capable of testing components in bending, compression, and shear modes. As part of the DOE door project, component tests under dynamic test conditions were performed on a composite hat section, MAT 54 material card was recalibrated and we found a good agreement between experimental and simulation results.
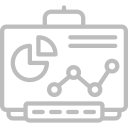
Characterization Services
Services include thermal/chemical characterization and component testing; sub-assembly testing/validation; and NADCAP compliant testing.
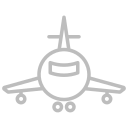
Industry Production
Clemson Composites Center caters to the aerospace, automotive, consumer, medical and defense industries.

System Components
Characterization ranges available include lay-ups, prepregs, resin systems, adhesives, and reinforcements.
05
SERVICES
COMPOSITES 4.0
Just as manufacturing has evolved through the Industrial Internet of Things (IIoT), plastics and advanced materials can improve with the addition of cyber-physical systems, advanced analytics, and predictive processes.
INDUSTRIAL SCALE SOLUTIONS
Termed Composites 4.0, the integration of traditional and cutting-edge technologies is particularly challenging due to the inherent complexities in composites manufacturing. CCC provide services and expertise that are needed to overcome these challenges and implement Composites 4.0 at research and industrial scale.
CCC helps customers accelerate material development process using its data-gathering infrastructure and data analytics techniques. We use Artificial Intelligence (AI) methods backed with chemical and physical relations to find more promising development directions and better optimize the material composition and processing parameters. This will ultimately lead to shorter and more economic material development.
Composites manufacturing is knowledge-intensive. At CCC we help you enable smarter manufacturing by using intelligent tools and sensors to capture the data, fuse it together, and use this information to improve the manufacturing process and maximize profitability.
Applying Composites 4.0 can be difficult with the aging infrastructure and older equipment, but there is an easier and cost-efficient way than just replacing this equipment. CCC provides help with the application of smarter components that can be retrofitted to your current systems to make them Composites 4.0 enabled.
The access to world-class characterization equipment and seasoned research engineers has also enabled CCC to reverse engineer materials for a host of applications.
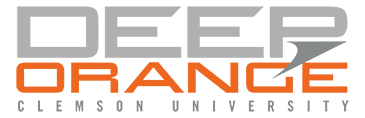
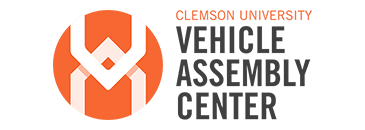
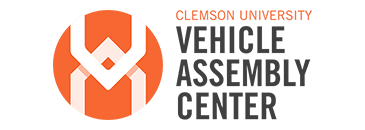
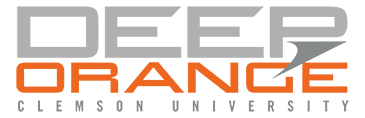