STATE OF THE ART
ADVANCED MATERIALS
INNOVATIONAL. Clemson Composite Center is pioneering research and product development to transform the future of sustainable technologies.
STATE OF THE ART
MOVING FORWARD
Innovation. Development. Sustainability. Clemson Composites Center transforms technological research into an educational powerhouse. Spurring economic development, the Center focuses on key sectors that will have an impact throughout South Carolina and the country.
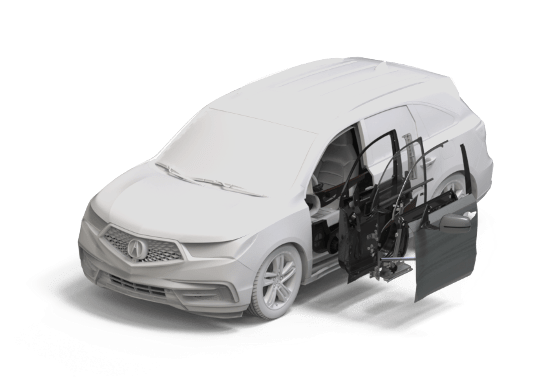
I purposefully focus on developing cost-effective and efficient yet sustainable technologies that benefit the four key sectors in human habitat, i.e. education, industry, society and environment. My philosophy is simple, anything I develop has to benefit them.
– Srikanth Pilla, Jenkins Endowed Professor
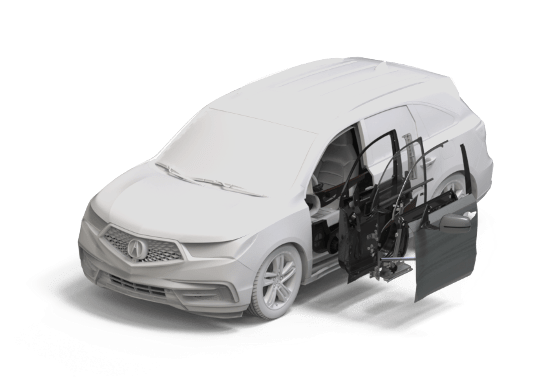
I purposefully focus on developing cost-effective and efficient yet sustainable technologies that benefit the four key sectors in human habitat, i.e. education, industry, society and environment. My philosophy is simple, anything I develop has to benefit them.
– Srikanth Pilla, Bosch and Jenkins Endowed Professor
CLEMSON COMPOSITES
We are a research, innovation, and development facility aimed at enabling lightweight, composites-intensive transportation systems.
A COMPOSITE IS THE COMPLEX UNION of different elements to create a stronger or superior product. Some of the first results involved the use of mud and straw to reinforce pottery and boats. Clemson Composites Center continues the economic advancement of materials by focusing not only on innovative research but on sustainable applications.
SUSTAINABILITY
Beyond reducing the weight and cost of vehicle components, our analysis looks at how the technology can be reused. Applications could filter into numerous industries, including home appliances. Composites and polymers made of biorenewable products could mean that parts are recyclable and reduce environmental impacts.

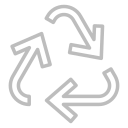
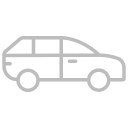

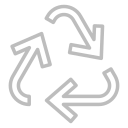
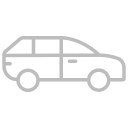
ENERGY SAVING
LIGHTER DOOR OPENS ENDLESS POSSIBILITIES
Lighter. Stronger. Cost-effective. Composite materials offer new ways to increase fuel efficiency while meeting or exceeding performance, safety, quality and production volume.
CARBON FOOTPRINT
TREAD LIGHTLY: FOOTPRINT REDUCTION
From incorporating recycled or recyclable materials to determining ways to improve fuel efficiency, sustainability is key throughout the entire manufacturing lifecycle.
WHY CLEMSON COMPOSITES
Full-spectrum development capabilities that span from theory to validation. We can help in every phase of the manufacturing process.

DESIGN & ENGINEERING
Expertise to transform fundamental research into full-scale concepts
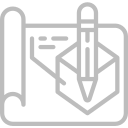
MATERIAL DEVELOPMENT
Manufacturing and research department who pioneer innovation
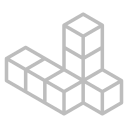
MANUFACTURING
State-of-the-art manufacturing equipment to solidify ideas
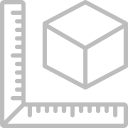
CHARACTERIZATION
Detailed analyses of projects from continual validation and testing
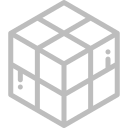
APPLICATION
Product development partnerships with industry and research centers
DEEP EXPERTISE
Advanced materials are crucial to a sustainable future across every industry, and Clemson Composites is here to help. Learn how we’re solving problems and driving innovation for our partners today.
ULTRA-LIGHTWEIGHT
ENERGY
Clemson University researchers began work for a $5.8 million grant from the U.S. Department of Energy to pioneer technology for fuel-savings, energy efficiency, and to meet the U.S. corporate average fuel economy standards. Working with industry partners, the Clemson team engineered and constructed an ultra-lightweight thermoplastics composites door that enables innovation for greenhouse gas reduction, recyclability, and circular economy.
BLENDING METHOD
AEROSPACE
The encapsulation of aqueous cargo is a widely recognized challenge, despite its industrial value for numerous applications, ranging from self-healing and drug delivery to cosmetics and pesticides. Clemson researchers adopted novel surface grafting methods to evaluate the impact of the graft characters on the properties of the Cellulose nanocrystal nanocomposite. The study demonstrated an effective method to encapsulate a hydrophilic payload.
STREAMLINE BUILD
MOBILITY
Hybrid Single-Shot manufacturing can help reduce the time and cost it takes to produce components composed of dissimilar materials and need to be joined together. The process is aimed at streamlining the manufacturing of some components, such as the center consoles in cars. One of the goals is to reduce the cost of making vehicles lighter, which improves mileage and helps automotive companies meet federal fuel efficiency standards.