hybrid single-shot process for metals and composites streamlines and increases cost savings in manufacturing
MOTIVATED BY THE CONCEPT of the integrative production systems, hybrid process of polymer injection molding and sheet metal forming, known as Hybrid Single-Shot (HSS), has been introduced to manufacture sheet metal-polymer components using a single tooling, machinery, and operating system. During this process, the sheet metal blank inside the injection mold is deformed by means of tool movement and/or by pressure of the polymer melt. As the melt cools, the injected polymer is permanently bonded to the deformed sheet metal depending upon the existence/use of any bonding agents.
DIGITAL TWIN
Invented by Clemson researchers Srikanth Pilla and Saeed Farahani, the novel process can help reduce the time and cost it takes to manufacture components that are composed of different materials and need to be joined together. The process is aimed at streamlining the manufacturing of some components, such as the center consoles in high-end cars.
GOALS AND METHODOLOGY
One of the goals is to reduce the cost of making vehicles lighter, which improves their mileage and helps automotive companies meet federal fuel efficiency standards. But researchers said the technology could be used in a variety of industries, including home appliance manufacturing.
The new method could reduce infrastructure costs and cycle time, while helping ensure that the pieces are mistake free and fit snugly together. The technology could be ready for the manufacturing floor in as little as two years.
When some parts are made conventionally, one machine stamps sheet metal into the desired shape, and another machine creates polymer or composite parts. Then the pieces are bonded together with glue.
In hybrid single-shot manufacturing, it’s all done in one machine. The technology can be used in existing equipment, obviating the need for major capital investment, Pilla said.
As part of the research, Farahani built a “concept design tool,” and covered it with sensors that measure everything from temperature to pressure. He also created his own software that allows researchers to create a computer model of the machine’s process, also called a “digital twin.” The digital twin coupled with artificial intelligence is playing a crucial role in teaching the machine to operate on its own.
Researchers also plan to test the new technology at the Clemson Composites Center with the goal of making real components.
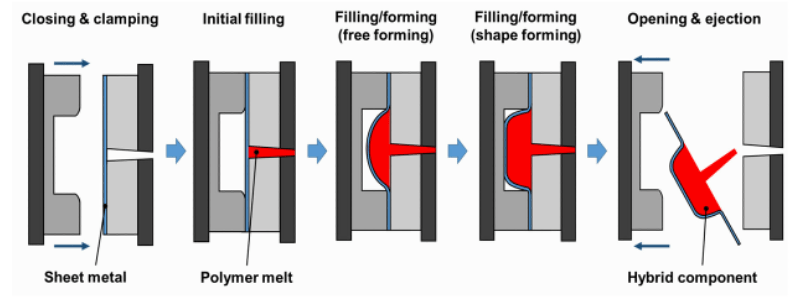
Publication Links
- Numerical Simulation for the Hybrid Process of Sheet Metal Forming and Injection Molding Using Smoothed Particle Hydrodynamics Method
- Feasibility Study for Manufacturing CF/Epoxy – Thermoplastic Hybrid Structures in a Single Operation
- Clemson University Automotive Engineers Invent ‘Single-Shot’ Manufacturing Technology